Toothed metal lids have long been a part of the image of mineral water, beer, lemonade and other drinks in glass bottles. Not everyone knows that this device, called crown cork, has its own history, a number of types and wide application possibilities.
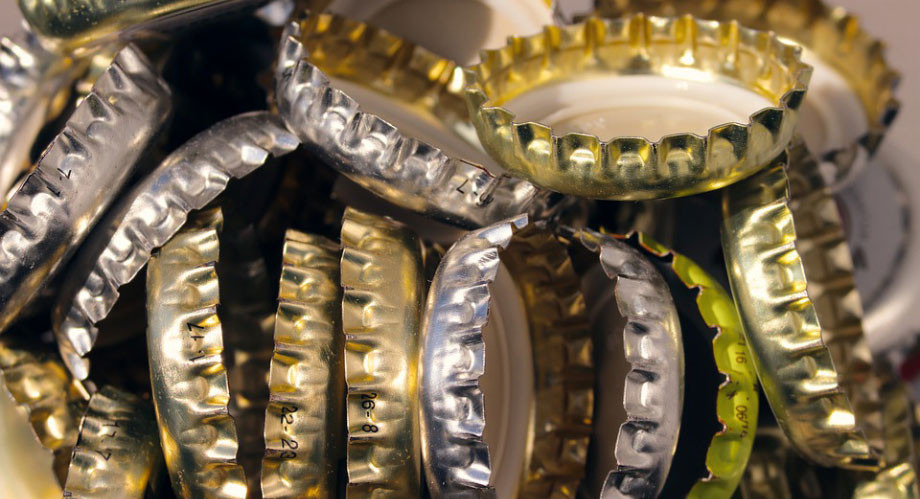
What is crown cork and how did it appear?
Crown cork is a specialized product for capping glass bottles, it consists of a metal base and a gasket. William Paintner, an inventor, patented the crown cork in 1892.
The craftsman was inspired to create the product by the growing popularity of carbonated drinks, which at that time were sold exclusively in bars and pharmacies. Due to the lack of a suitable closure, which would preserve the effervescence and other properties of the drinks, it was impossible to bring them home. For the cork design, Paintner used a metal base and a layer of natural cork. The invention has gained demand among food manufacturers, and does not lose its relevance to this day. Subsequently, Paintner also developed the first crown cork capping machine.
Crown Cork Today: Varieties and Their Applications
Today these types of lids are especially widely in demand by companies that produce mineral water, soft drinks, beer and other non-alcoholic, low-alcohol and carbonated drinks. Manufacturers give preference to this kind of capping, since crown corks have a number of advantages over other closures:
· It is reliable. The metal version ensures the strength of the package, allowing preservation of the taste and other qualities of the liquid in the container.
· Provide complete tightness. The curving part of the lid (the so-called "skirt") is adjacent to the neck as tightly as possible, which allows achieving absolute impermeability of the container.
· They are inexpensive. The price of crown corks is significantly lower than standard screw caps.
· They have options for a variety of design. Crown corks are used as full-fledged advertising platforms and allow applying various original design solutions.
Modern manufacturers work in conditions of fierce competition, so they constantly improve both the product itself and its packaging. Starting from creation of crown corks, there have been a number of changes that primarily affected the component materials: the cork seal in the lid was replaced with a more practical plastic one. Main design changed repeatedly and it expanded due to a variety of functional devices for additional ease of use of corks by consumers.
The following types of crown corks are best known today:
· Classic pry-off. The easiest and cheapest option for capping glass bottles. Opening is done with an opener.
· Twist off. In this version, crimp teeth are completely eliminated, and the inner surface is supplemented with a special guide, due to which opening occurs. The widespread use of the cork is explained by its convenience: no special devices are needed to open.
· Ring-pull crown. Cork models complemented by a finger ring for easy and quick opening. You can especially find it on beer bottles.
· Flip cork. Reusable cork with aluminum frame and ceramic cork. These caps are used to seal premium-bottled drinks, as well as containers used in scientific laboratories for sampling.
The production of crown caps is carried out in accordance with the requirements of GOST (government standards):
Based on these and other regulations declared by industry standards, the production of appropriate capping equipment is carried out.
How does crown corks capping work and what are the features of this process?
Bottles are capped with crown corks by means of crimping. The main technological complexity of this process is to achieve the optimal balance between tightness, aesthetics and ease of subsequent opening. Manually, this is practically unrealizable, but it is quite possible for specialized equipment. Today, the market has a wide selection of semi-automatic and automatic machines that perform the crimping operation efficiently and with high productivity.
In order to better understand how these units work, we suggest that you first examine the equipment device using the classic semi-automatic capping machine model MZ-400K, manufactured by our “AURORA PACK ENGINEERING” factory.
The capper consists of the following main components:
· Frame. It serves for fixing the main units of the capper on it. It contains adjusting holes in a vertical plate for installing the driving head and level stop;
· Crimping mechanism. It is designed for capping bottles with a cap and rolling it further with a whisk 26 N 180 for the crown cork. The crimping mechanism consists of a pneumatic cylinder (item 1) and a crimping head (item 2);
· Limit stop (item 3). It is designed for accurate alignment of containers in accordance with their diameters;
· Countertop (item 4). It is designed to accommodate containers.
· Chokes (item 5). They serve as elements for adjusting the speed of lowering and raising, as well as for smoothness of the descent and raising of the driving head;
· Casing (item 6). It performs the function of a protective fence;
· Pedal (item 7). It is a control element. When pressed, the pneumatic cylinder of the crimping mechanism actuates.
The principle of operation of this and other similar machines (for example, the semi-automatic closure MZ-400RPM Kronen) is approximately identical. The capping cartridge lowers to the level of the container and presses the cork to the neck. A special spring (whisk) of the head presses on the edges of the cork, bending them down. The gaps between the formed denticles are crimped around the upper edge of the neck. At the end of the process, the cartridge returns to its original position, and the corked bottle is removed from the machine.
In automatic equipment for capping containers with crown corks, the operations of feeding and removing bottles are carried out without human intervention. In particular, in an automatic machine for sealing glass containers with crown corks, the movement of the bottles is performed by a rotary disk with a step-by-step principle of operation. Such a rotational system ensures continuous cycle repetition in accordance with the speed of the entire packaging line into which it is integrated. The equipment is designed specifically for these types of corks, it demonstrates stability and develops output up to 2200 units per hour.
For high quality sealing with crown corks, the integrity and dimensional conformity of all the components involved in the process (the cork, the neck of the container and the crimp cone) are especially important. If any element is damaged or manufactured in an inappropriate format, mechanical defects may occur during crimping. Too small a diameter of the crimped cork can lead to difficulties in opening the container, and too large one can lead to the loss of tightness. These and other details require constant monitoring, especially at enterprises with production lines, where a failure of one system can lead to the shutdown of the entire complex.
Therefore, crown cork capping is a simple, low-cost and at the same time effective technology, which, like any other, has a number of its own characteristics. Modern equipment allows you to achieve all the necessary indicators of tightness, while ensuring a neat appearance of the package. When choosing a suitable installation, such criteria as the format of the packaging used and the volume of corked products come to the fore. When using non-standard bottles and crown corks, we recommend giving preference to individually designed models.